Introduce the sand and gravel production line process in detail
The sand and gravel production line equipment is mainly composed of vibrating feeder, jaw crusher, impact crusher, vibrating screen, belt conveyor and other equipment. In order to meet the different processing needs of customers. It can also be equipped with cone crushers, dust removal equipment, etc.
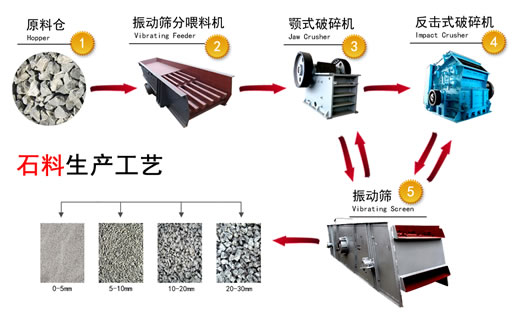
Introduce the sand and gravel production line process in detail:
The large stones are evenly sent to the jaw crusher by the vibrating feeder through the silo for coarse crushing. And the coarsely crushed stones are sent to the impact crusher by the belt conveyor for further crushing.
The finely crushed stones are sent to the vibrating screen by the belt conveyor for screening, and several different specifications of stones are screened out. The stones that meet the particle size requirements are sent to the finished product pile by the finished belt conveyor.
The stones that do not meet the particle size requirements are returned by the belt conveyor. And sent to the impact crusher for re-crushing, forming a closed circuit for multiple cycles. The particle size of the finished products can be combined and classified according to the needs of users. In order to protect the environment, auxiliary dust removal equipment can be equipped.
Sand and gravel production line performance characteristics:
Simple operation, advanced electronic control system, high degree of automation, simple process of the whole sand and gravel production line, easy to operate. Except for switching on and off and daily maintenance, no manual operation is required.
High economic benefits, overcoming the shortcomings of high production costs caused by serious wear and tear of traditional sand and gravel production equipment when processing hard materials, large output, high production efficiency, low operating costs, and high economic benefits.
The quality of the finished product is good, which solves the fatal problem of unqualified grain shape of the finished sand and gravel processed by traditional equipment. The finished stone has good quality, uniform particle size, good grain shape, and low stone powder output rate. Which fully meets the national highway material requirements.