What crusher equipment to choose for crushing iron ore?
Analysis of iron ore properties
Iron ore is an important raw material for iron and steel production enterprises. Natural ore (iron ore) gradually selects iron through procedures such as crushing, grinding, magnetic separation, flotation, and gravity separation. Iron ore is a mineral aggregate that contains iron element or iron compound and can be used economically. Any ore containing iron element that can be used economically is called iron ore.
The iron ore crushing process generally adopts several processes of feeder, first crushing, secondary crushing, screening, fine crushing and dry separation. The higher the percentage of stone that is dry selected. Some small concentrators directly dry the iron ore crushed by the fine jaw crusher, resulting in a serious waste of natural resources.
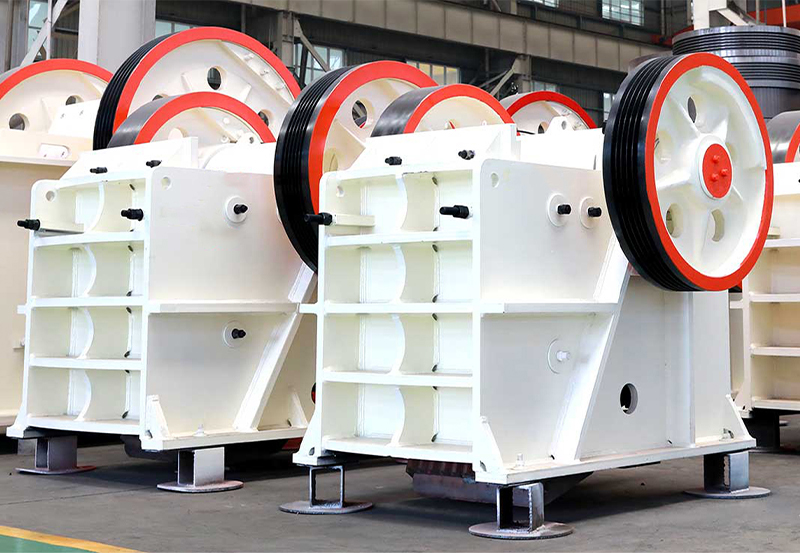
Different stages require different crusher equipment
Head crushing:
JC series jaw crushers are generally used for head crushing in iron ore production operations, and GC series gyratory crushers can be used in large production units. Jaw crusher is the most traditional and most stable and reliable primary crushing equipment, and has the widest application range.
Secondary crushing:
In the iron ore crushing production process, GPY series cone crushers are generally used for secondary crushing. The structure of cone crushers is relatively complex and the equipment value is high. However, its output is larger, the crushing particle size is smaller, and the service life of wear-resistant parts is longer. Therefore, cone crushers are widely used in relatively large iron ore dressing fields. From the production efficiency and cost of iron ore, the use of cone crusher can effectively reduce the production cost. Because the cone crusher can provide a smaller product size, from the overall process, the use of lamination equipment to complete the main crushing task of iron ore is the most economical production method.
Fine crushing and screening:
The screening equipment generally adopts YKR series circular vibrating screen to screen the materials after the second crushing. Generally, materials with a size of 10mm or less can be screened for dry selection. After screening, materials with a size of 10-40mm enter the fine crusher for fine crushing. Of course, the particle size range of screening can be adjusted according to the actual situation, in order to achieve the most economical operation mode.
Fine crushing:
PLS series vertical impact crusher is generally used for fine crushing, which adopts the principle of stone hitting stone and stone hitting iron. After entering the crushing cavity, the crushed stone is repeatedly broken until the fine sand is discharged from the discharge port. There are no problems such as frequent shutdown, blockage of sand and gravel, and the motor does not move. It not only simplifies the production process, but also the design of the deep cavity impeller increases the throughput of materials by more than 30%, and the operation rate is high during work, which greatly improves the production.
Summarize
Different uses require different crusher equipment, and better benefits can only be brought about if the production needs are met.