Sand and gravel production line – how to control the quality of machine-made sand production?
The manufactured sand produced by the sand and gravel production line can be used in many industries. The manufactured sand used to prepare mortar has strict technical requirements, which mainly include: (1) the content of harmful substances is low, and there is no potential alkali activity; (2) the particle gradation is excellent, and Good grain shape and low crushing value; ③ moderate stone powder content and low mud content.
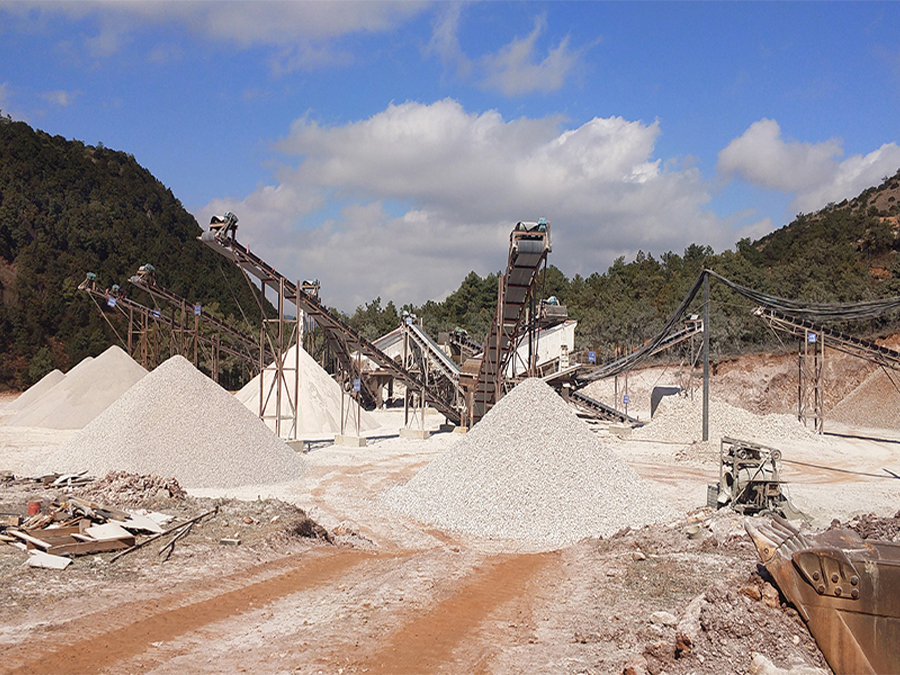
The machine-made sand produced by the sand and gravel production line is still in its infancy in the whole country, and the guarantee of its quality is even more important.Compared with natural sand, the quality of manufactured sand has a greater impact on mortar and concrete.
On the one hand, machine-made sand has its quality advantages, which are reflected in three major characteristics: stable quality (fixed source of production, mechanized production), reasonable and adjustable particle gradation, and rational use of stone powder; on the other hand, machine-made sand also has inherent deficiencies.
Diverse types, large specific surface area, and large water demand, such as the particle shape is mostly triangular or square, rough surface, sharp edges and corners, it will affect the workability (but it is beneficial to the strength), such as a long needle flake shape, it will affect the workability. Both sex and strength are bad. Therefore, the quality of machine-made sand should be guaranteed from the source of production. To obtain machine-made sand with good quality, in addition to designing a reasonable production process and selecting corresponding professional equipment, the following quality control work must also be done.
(1) Selecting the parent rock and mine, mining the mine rationally, and controlling the chemical composition and mineral composition of the parent rock of harmful substances determine whether the machine-made sand contains harmful substances and whether there are potential alkali aggregates.
At the same time, there is a direct relationship between the strength of the parent rock and the crushing value of mechanical properties. Therefore, the mechanical properties and chemical properties of the parent rock should be evaluated first, and the parent rock that meets the requirements should be selected. It is generally required that the strength of the parent rock is not less than 80MPa.
During mining, soil, weathered rock, tree roots, turf and other debris should be prevented from being mixed into the boulders. Among them, the control of soil is particularly important. The mud content in the machine-made sand mainly comes from the mud entrained by the boulders. To control the mud content in the machine-made sand, the following work must be done: ① When mining the mine, the surface vegetation and soil should be removed; ② During the loading and unloading process of the block stone, the soil should be prevented from mixing; ③ When there is a lot of soil mixed in the block stone, artificial Pick out the ore; ④The block stone should pass through the vibrating feeder to further screen out the soil.
(2) Optimize the production process parameters of the sand and gravel production line. Strengthen equipment maintenance, and stabilize the gradation of machine-made sand.
To obtain machine-made sand with excellent gradation and stability. The production process parameters must be optimized according to the characteristics of the equipment. Such as feed size, speed, discharge Feed width, etc.
Among them, the size requirements of the crushed stone entering the sand making machine are easily overlooked. Generally, the technical parameters of the equipment only indicate the large particle size of the machine. Which is generally 40 to 60mm. In fact, there is a good particle size range, which is generally around 20mm. If the particle size of the man-machine is too large. Not only the coarse gradation of the sand produced is not good. But also the output is low and the energy consumption is high; if the particle size of the man-machine is too small. Not only the fineness of the sand is fine, but also the content of stone powder is large.
In actual production, the super-sized materials are usually crushed in the secondary stage and enter the sand making machine. So that the sand making machine is used as a crusher. Which is one of the reasons why the machine-made sand is coarse. Therefore, it is necessary to determine the optimal range of crushed stone size through experiments to obtain good product quality and low energy consumption.
In addition, attention should also be paid to the angle of the vibrating screen and the size of the screen hole. Generally, the maximum inclination angle of the circular vibrating screen should not exceed 25. The size of the sieve hole (square hole) should not exceed 3.5mm. In order to control the maximum nominal particle size of the machine-made sand not to exceed 4.75ram. And the fineness modulus to be less than 3.4. At the same time, it is necessary to strengthen the maintenance of the equipment to ensure the normal working condition of the equipment. It is worth mentioning that the wear of the lining plate and hammer head should be paid attention to and replaced in time.
(3) Take effective measures to strictly control the content of stone powder.
The content of stone powder in the machine-made sand from the sand making machine is generally about 15%. How to remove and control the excess stone powder in the machine-made sand is one of the key technologies in the production of machine-made sand. The methods currently used mainly include dry dust collection and wet water washing.
①Dry dust collection. Dust collection is to eliminate the environmental pollution caused by dust in the production process of machine-made sand. However, by reasonably arranging the dust collection points and adjusting the air volume and air pressure of the vacuum cleaner. The stone powder in the machine-made sand can also be partially selected. In the actual production process, a dust collector with good dust collection effect should be selected. And the working parameters of the dust collector should be determined according to the requirements of the stone powder content in the machine-made sand. Due to the study of this project. The limit of stone powder in grade III manufactured sand has been relaxed from 7% to 10%. So that the production of grade III manufactured sand can be produced by dry dust collection process. Which can undoubtedly save water and reduce pollution.
② Wash off the powder with water. Washing and removing powder from machine-made sand is the key technology for producing high-quality machine-made sand.