How does the product quality of the sand and gravel production line reach the standard?
Conventional calculation method and disadvantages of sand and gravel production line stock yard selection.
The conventional method for the selection of natural sand and gravel quarries and the calculation of mining scale is based on the mining and transportation conditions of each quarry. Evaluation is carried out separately. Through analysis, several combination schemes are drawn up, aiming at less waste materials. material balance calculation.
In the design of sand and gravel systems in most large and medium-sized water conservancy and hydropower projects in China. Only a single stock yard is used as a mining plan, and a simple balance calculation is performed. And a stock yard with less waste materials is selected as the mining plan. Single stock yard mining is implemented.
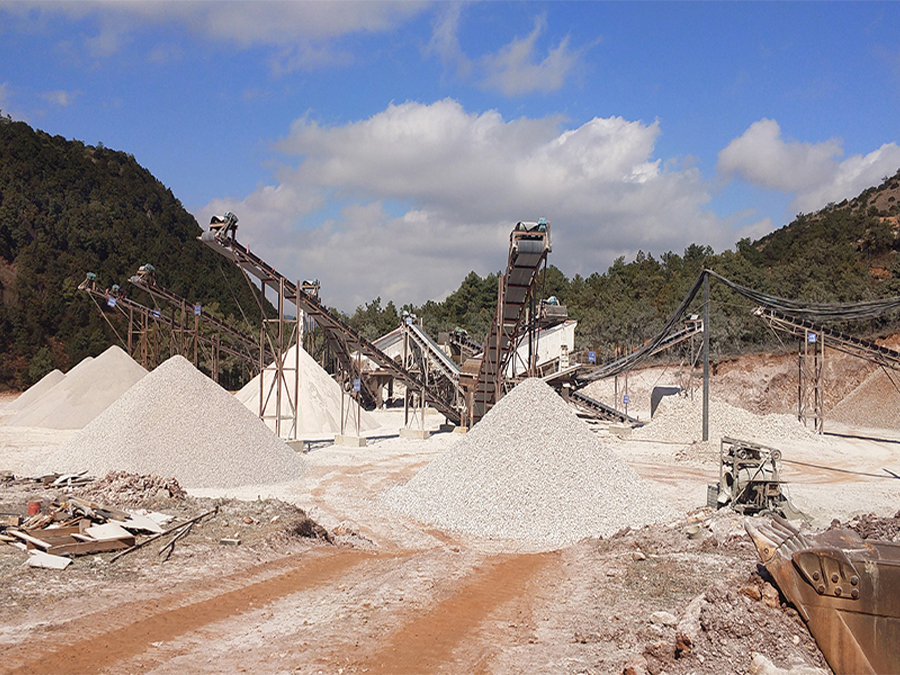
The main drawbacks of this approach are:
(1) Due to the different mining conditions, distances and mining methods of each stock yard, the civil construction cost and aggregate mining cost of each stock yard are also different. The mining combination plan selected with the goal of less waste material may not be the one with low total mining investment.
(2) In each combination scheme, first draw up the mining ratio, then calculate the amount of discarded material, and then select the optimal combination scheme. It is not a combination mining in the true sense. Because. When the mining ratio is further changed in a combination scheme, it is also possible to find a combination scheme with less waste material.
(3) For the adjustment of the grading sand and gravel system, first select the mining combination plan with less waste material according to the conventional method, and then calculate the scale of the crushing and processing of the aggregate to determine the processing capacity configuration of the equipment. It is difficult to select the mining combination scheme with low comprehensive investment in mining and processing.
(4) After the combined mining plan is determined. The mining plan is often formulated according to the method of mining each material field one by one in most projects. There is no real implementation of simultaneous mining of multiple material fields in proportion. Due to the combination scheme, the aggregates of some stockyards are too coarse, and the aggregates of some stockyards are too fine. The implementation of step-by-step mining will easily lead to unbalanced crushing and processing capacity. And the capacity configuration of crushing equipment is too large, causing unnecessary aggregate waste. repair.
Conventional calculation method and disadvantages of grading adjustment of sand and gravel production line
For the sand and gravel system that adjusts the gradation. The conventional calculation method of the gradation adjustment is based on the mining combination grading. And the total amount of aggregate mining is equal to the total demand. Carry out the calculation of the surplus and deficiency of aggregates at all levels; Type and processing capacity. From rented aggregates to fine aggregates, the aggregate surplus and shortage are adjusted step by step. And the scale and equipment configuration of each level of crushing are finally determined. When there is a shortage of large-diameter aggregate during the calculation process. This grade of artificial aggregate or commercial aggregate can be used to supplement. The main drawbacks of this approach are:
(1) The conventional calculation method of grading adjustment based on the premise of equal mining is still the method of mining and processing subsection calculation. It is difficult to select a mining and processing combination scheme with low total cost of mining and processing.
(2) In the selection of a certain level of crushing equipment, there is a lack of optimization target guidance. It is difficult to avoid blindness. Because by changing the type of crushing equipment at this stage, the yield of crushing products can be changed. It is possible to reduce the total number of crushing segments and effectively reduce the fixed investment cost of crushing equipment.
(3) The computational workload is large.