Precautions for operation and maintenance of sand making machine impeller
The sand making machine manufacturer reminds the sand making machine what points should be paid attention to in the operation and maintenance of the impeller. The dryer is composed of a horizontal cylindrical cylinder, an exhaust pipe, a feeding device, a discharging device, a screw device inside the cylinder, a cleaning device, a material shifting plate, an air induction device, a transmission device, a dust removal device and an electric control device.
Sand making machine is a special equipment for producing sand and stone for construction.
It can crush all kinds of hard rock metal and non-metallic ores into construction sand and gravel materials of various particle sizes. The sand has uniform particle size and high compressive strength. It is ideal for stone shaping, artificial sand making, refractory materials. Advanced equipment in the fields of ball mill feeding and industrial ore product processing.
Common stone crushers mainly include jaw crusher, mobile crushing station, impact crusher, impact crusher, compound crusher, single-stage hammer crusher, vertical Type Crusher, Gyratory Crusher, Cone Crusher, Roller Crusher, Double Roller Crusher, Roller Crusher, Ball Mill, Raymond Mill, Sand Making Machine, Sand Washing Machine, High Pressure Suspension Roller Mill, etc. .
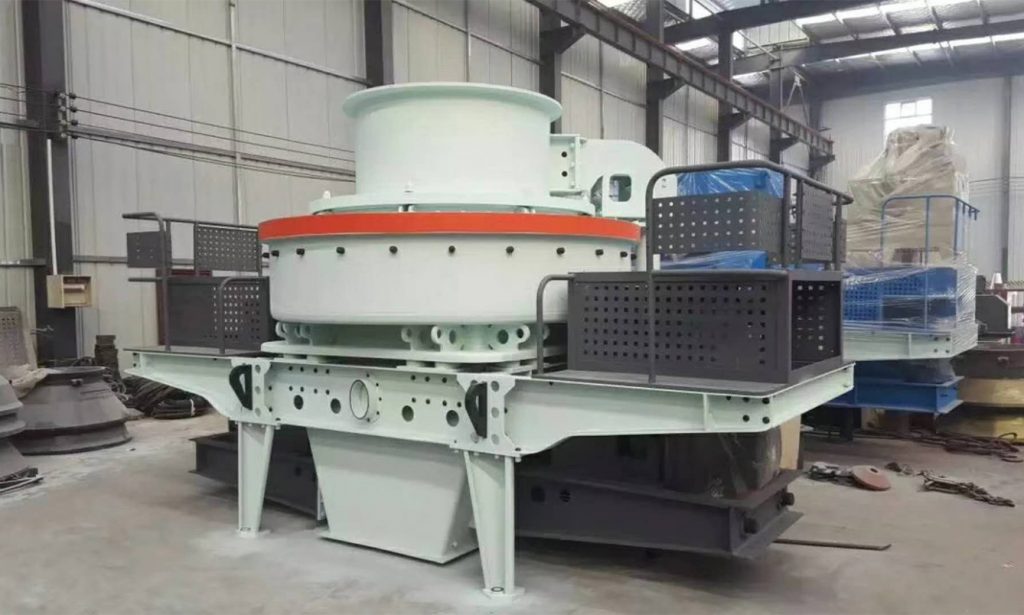
The sand making machine is suitable for crushing and forming soft or medium hard and extremely hard materials. It is widely used in various ores, cement, refractory materials, bauxite clinker, corundum, glass raw materials, machine-made building materials, gold slag, especially for carbonization High-hard, extremely hard and wear-resistant materials such as silicon, corundum, sintered bauxite, and American sand have higher output efficiency than other types of crushers.
What work points should be paid attention to in the operation, management and maintenance of the impeller of the sand making machine:
The impeller is installed on the upper end of the main shaft assembly of the sand making machine. The transmission button distance is connected by a tapered sleeve and a button, and rotates at a high speed. The material enters the center of the impeller through the central feeding pipe of the feeder on the upper part of the impeller.
The impulse accelerates the material to a certain speed and shoots it out, the impact material lining is strongly self-shattered in the vortex break cavity, and the impulse cap and wear-resistant block are installed between the upper and lower channel plates to protect it from abrasion. When the sand making machine stops operating, attention should be paid: before the discharge equipment stops feeding. The feeding should also continue to be uniform. And the material specifications must strictly comply with the requirements, otherwise it is easy to wear due to the material.
The sand making machine generally adopts a belt transmission mechanism driven by a single motor or a double motor. The two motors are installed on both sides of the main shaft assembly respectively. The pulleys of the two motors are connected to the main shaft belt to balance the forces on both sides of the main shaft without increasing the torque.
The impeller is an important part of the sand machine. And it is also the most vulnerable part of the sand machine. Since the material is distributed and emitted in the impeller. If it is not operated properly, it is easy to cause wear of the impeller material. Therefore, when a series of careless production accidents occur, special attention should be paid to specific work and operations.
It is suggested that the operator can optimize the workflow from the following aspects:
1 When the discharge equipment stops, the feeding should be stopped in time, otherwise. The impeller will be crushed and a motor will be burned.
2 The feed particles are strictly in accordance with the specified requirements, and materials larger than the specified materials are prohibited from entering the crusher, otherwise it will cause unbalanced impellers, excessive wear of the impellers. Blockage of the impeller channel and the central feeding pipe, and make the crusher unable to work normally.
3 Check the wrongdoer’s rotation direction from the direction of entry. The anti-seepage should be opened counterclockwise, otherwise the motor wiring should be adjusted.
4 Before closing the door, observe whether the material is unscrewed from the warehouse.
5 The starting sequence of the sand making machine and conveying equipment is:
the sand discharger feeds, the crusher must be started with no load, and only after the crusher is in normal operation can the material be fed. Closing a program is the opposite of starting a program.