How to make full use of the effect of the sand making machine
The sand making machine designed and manufactured by our company has the advantages of small discharge particle size, uniform particle shape, large production capacity, long life of the hammer head, small supporting power, changing from three-stage crushing to two-stage crushing, simplified process, simple structure, and easy maintenance. Convenience, stable operation and so on.
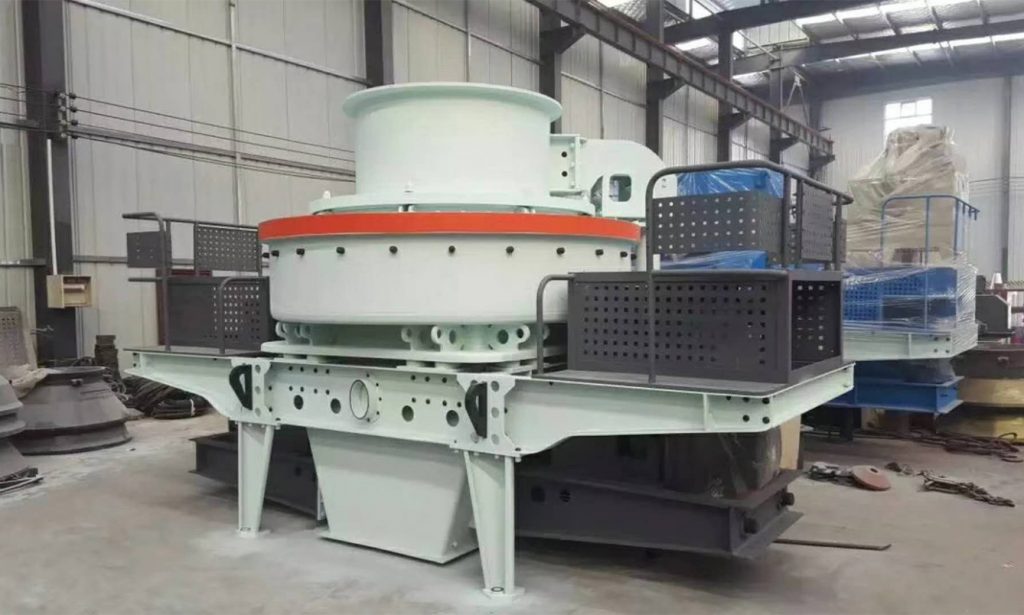
But how can we achieve the maximum effect of the sand making machine?
First of all, you should pay great attention to the installation details of the machine during installation:
1.When assembling the high-fine crusher, it is necessary to pay attention to maintaining the dynamic balance of the rotating parts such as the main shaft and the drum. The hammer frame and the hammer head, and the weight deviation of the ring-balanced hammer head must not exceed 0.2 kg.
2.When the high-fine crusher and motor are installed on the concrete foundation, ensure the levelness of the main shaft and the plane of the two pulleys, the deviation shall not exceed 1mm. When designing the installation foundation, the feeding space and maintenance space should be fully considered.
3.The bolts of each assembly of the fine crusher must be tightened, and the gap between the machine base and the side cover must be tight to prevent ash leakage.
4.When installing the lower box, install the liners on both sides of the lower box first, and then install the grate frame.
5.The user can operate after making and installing the driving wheel, driven wheel, and V-belt safety cover according to the actual terrain.
Secondly, pay attention to the correct operating procedures of the machine during the test run:
1.Turn the V-belt to rotate the main bearing for 2-3 turns, and start the motor after confirming that there are no obstacles in the machine;
2.Run continuously without load for 2-4 hours, stop the machine for inspection. The temperature rise of the bearing is normal (below 70°C), all parts are connected tightly. And there is no abnormal phenomenon.
Again, the operation and maintenance of the machine cannot be ignored, and should be strictly required:
1.During operation, it is strictly forbidden to enter hard objects such as iron blocks into the fine crusher. If abnormal sound is found, stop the machine immediately for inspection;
2.Start-up sequence: start the discharge conveyor – start the fine crusher – start the feeder.
3.Shutdown sequence: turn off the feeder — turn off the fine crusher — turn off the discharge conveyor.
4.Requirements for changing shifts: This equipment is generally operated in three shifts. When shifting, it is required to open the side cover for inspection and tighten the bolts of the hammer head. If the hammer head is found to be worn. It can be turned around and used or replaced with a new hammer head according to the situation, and the wear of the grate is checked. When taking over the shift, observe the condition of the equipment. After confirming that there is no problem, close the side cover and operate in sequence.
5.If it is found that the particle size of the product becomes thicker during the operation. Mainly check whether the grate and the grate have fallen off, etc., and should be reinstalled in time.
6.When replacing the grate, the ball press dryer needs to open the side cover of the upper box, remove the grate, and then replace the grate.
7.According to the nature of the material, the particle size requirements of the product. And the wear of the wearable parts, establish a large, medium. And small regular maintenance system to ensure the normal operation of the equipment.
Completing the above detailed requirements can better guarantee the efficiency and service life of the fine crusher!