What should be paid attention to in the layout of sand making machine production line
The production process of sand making machine production line is roughly: (silo) -> vibrating feeder -> jaw crusher -> impact crusher (optional) -> impact crusher -> vibrating screen -> sand washing Machine->(finished sand), each equipment is connected by chute or belt conveyor. The designed output is generally 50-500 tons/hour.
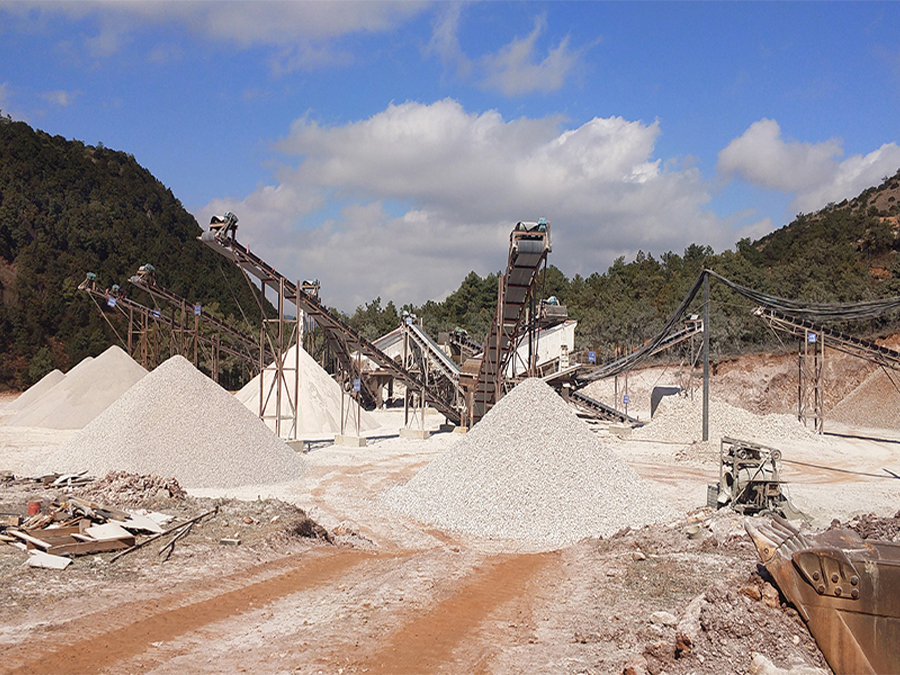
Today, tell us about the precautions for the placement of the sand making machine production line. I hope we can read it carefully, and it will definitely help you:
(1) For multiple sand making equipment of the same standard in the same operation, it should be arranged at the same elevation as much as possible to facilitate process change or equipment exchange.
(2) The service period of the special sand and gravel processing plant for engineering is only a few years. The crushing, screening and sand making workshops can generally adopt open-air equipment (constructors in the northern icy cold area are outside in winter). In order to facilitate management and avoid electrical equipment from getting wet, it can be partially covered. . In order to facilitate maintenance, the necessary lifting equipment (mobile or fixed) should be provided.
(3) All operating channels or pits that are 0.5m above or below the ground should be equipped with railings. Transmission parts should have protective covers to ensure safe production. The overhead height of the pipeline shall not be less than 2m.
(4) For equipment with operating parts (such as operating parts, operating wheels, gate valves, etc.). The height of the center from the floor (ground) surface is generally 1000-1400mm. When it is necessary to lower the setting, the distance from the floor (floor) board shall not be less than the larger rolling radius of the operating part plus 100-200mm, so as to facilitate the disassembly and maintenance of the parts.
(5) The width of the operating surface of the equipment, when one side of the equipment is a fixed equipment or a wall, the net width is generally not less than 1500ram. For small equipment or equipment that is not frequently operated, the clear width can be reduced to about 1000mm, but not less than 800ram. When two devices share one operating surface, the net width is generally 1500-2000mm.
(6) The floor (floor) slab should have a certain slope to facilitate scouring.
(7) Channel. The width of the primary channel is 1500-2000mm; the width of the non-essential channel is 700-1000mm; the sidewalk of the conveyor corridor is not less than 700mm, and the maintenance channel is 500mm.