What details should be paid attention to in the daily operation of jaw crusher
The jaw crusher machine is one of the widely used machines in today’s society, such as smelting, mining, building materials, railways, highways, water conservancy and chemical industries. In order to improve work efficiency without overloading, the editor has compiled the following content, let’s take a look. Starting from the jaw crusher itself, the first reasonable adjustment of the speed of the machine can improve the production efficiency. During the operation of the jaw crusher, the speed should not be adjusted too fast, which will make the crushed ore in the crushing chamber too late to discharge and cause blockage, which will not only fail to improve the efficiency, but also reduce the production capacity and increase the power consumption.
After installing the jaw crusher, check all the criteria carefully to make sure there are no problems. Before the no-load test run, turn the crusher flywheel once to ensure that it is unobstructed. The conditions for no-load debugging are as follows:
- 1. The no-load trial operation of the jaw crusher is not less than 4 hours, but the trial operation can only be completed after the bearing temperature is stable for 1 hour.
- 2. The V-belt must not snap or slide.
- 3. All screws and fasteners checked shall not be loose.
- 4. The bearing temperature shall not exceed 70c.
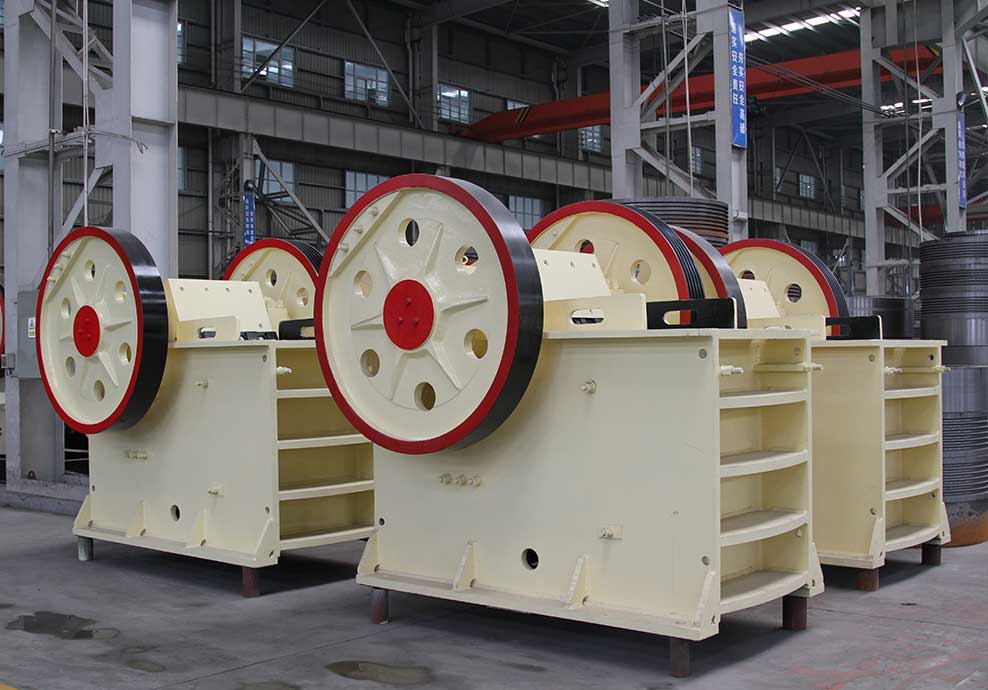
While ensuring the particle size of the product, the outlet should be adjusted reasonably so that the angle between the movable jaw and the fixed jaw is within a better range, which can also improve the production efficiency of the machine. In the later stage, more attention should be paid to lubricating and replacing parts that are easy to wear, and maintain the machine to keep the machine running smoothly. From the point of view of the materials to be crushed, the ore materials should not be too wet, if they are too wet, they will easily adhere to the jaw crusher, which will affect the feeding and conveying. Therefore, the moisture content of the material should be reduced before crushing, which can improve the production capacity. In short, in the daily operation of the machine, pay more attention to some small details, which will greatly improve the working efficiency of the machine.
Since the working principle of the jaw crusher is semi-rhythm, if too much material is put in, it will cause the material to be broken too late, and the broken material cannot be removed in time, resulting in sticky material. Therefore, either cutting or overfeeding affects productivity. Strictly control the amount of feed to prevent excessive blockage. Many companies blindly remodel silos in order to increase production capacity, which often leads to overfeeding. At the same time, rhythmic feeding is controlled to ensure the normal operation of the jaw crusher. At present, the crushing section of the mineral processing enterprise mostly uses the end chute for feeding, and two-thirds of the entire feeder is exposed outside the warehouse. Due to the remoteness of the feeding port, the feeder has completely turned into a vibrating chute, which not only has poor feeding speed, but also has serious wear and tear. The feeding position of the feeder should be within 1/3 of the top of the equipment, but vertical feeding is strictly prohibited to prevent the equipment from losing vibration ability or affecting the conveying effect under pressure.